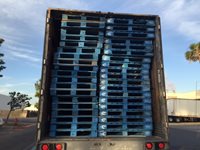
Having unloaded early on a Friday morning in Las Vegas, NV and eager to get loaded with the load I got heading back south towards home, I hustled to the pickup point for my next load. Knowing it was a load of pallets, I thought it would be a simple measure of pulling into some dirt pallet yard and loading up a full trailer of wooden material handling units. When I arrived, what I saw was quite to the contrary, it was a state of the art CHEP reconditioning plant. It is at facilities such as this that used pallets are brought in, assessed, and reconditioned to exacting industry standards, to be used again in the freight-handling world. Being that I was three hours early and the pallets were still being made for my order, I had a little bit of time to chat with Steven Sampson, Plant Operations Supply Chain Representative for the Las Vegas, Nevada CHEP facility.
Whether you have been trucking for many years, or are just getting started in this industry, I would put large sums of money that you have hauled a load, or seen a load being hauled, on CHEP pallets. It is hard to mistake these sturdy blue pallets when you see them and they are used very often to support many of the loads we carry as truckers. I had never given much thought into the world of the blue pallet, but being the inquisitive type, I was eager to converse with Mr. Sampson on just what goes on behind the scenes of the largest pallet pooling operation in the world.
Stemming from a way to handle WWII defense supplies more efficiently, the Australian government took post-WWII assets left behind by the U.S. Army in 1945 and combined it with its existing infrastructure to form the Commonwealth Handling Equipment Pool, or CHEP. Acquired by a materials handling company by the name of Brambles in 1958, CHEP has grown into the leader in many facets of the material handling industry. The four-way entry wood block pallet that we know best as truckers revolutionized freight handling when introduced in 1992 and has been boasted as “the perfect pallet” by many. It has even been compared to such other “perfect” innovations such as the paper clip and the mousetrap.
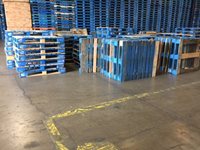
What really amazed me in looking behind the blue pallet process was the amount of data collection that goes on and quality control that is built into each one of these freight-handling marvels. Instead of just being scrapped when damaged, they actually replace worn and damaged component parts, enabling them to be as strong as new and completely reusable. Mr. Sampson liked to refer to them as “26 little components that can help transport anything more efficiently!” With their focus on reusability and stringent quality control from supplier to finished product, it is no wonder why Mr. Sampson showed such enthusiasm for CHEP as his employer. It is not too often you meet someone who truly enjoys what they do, especially in a warehouse scenario, but he was genuinely passionate about what his company is able to do for better freight handling solutions worldwide.
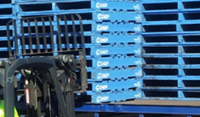
So the next time you pick up a load that is being forked around on one of these blue beauties, take a moment to think about some of the things that may go into it. Whether it is the trillions of data bytes used to track the pools themselves, or something as simple as the food-grade ink used to trademark each one of them with that distinctive logo, there is a lot more to these pallets than meets the eye. More than just wood, paint and nails, these pallets are truly our support system for getting the freight delivered safely!