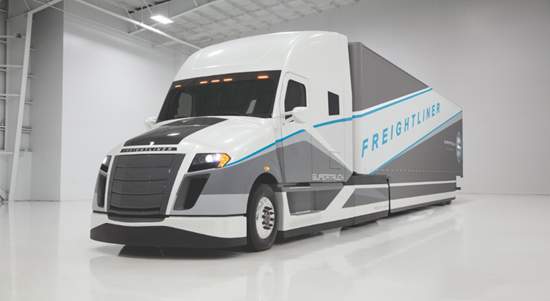 |
Integrated from the roof line to the pavement and front bumper to the rear ICC bar. |
This year at the Mid America Truck Show, I had the opportunity to step inside Freightliner’s SuperTruck. This unique truck was unveiled to the media at a press event in the Freightliner booth on Wednesday, March 25, 2015. I was thrilled to take an up close look at this incredible concept vehicle which will help shape the future of freight transportation.
I met with some of the top engineers who worked on developing the SuperTruck. We discussed the level of detail in which they researched and implemented many of the new technologies added to this truck. Some of their ideas came not only from a look into the future but a look back into the past as well. The grill shutters and the unpowered tag axle are just two examples of ideas pulled from history. Freightliner has already implemented some of these features into the new Cascadia Evolution. Two examples are the Cascadia Evolution Aerodynamic Package and the Detroit Integrated Power-Train.

Along with the SuperTruck, Freightliner included what could be called the SuperTrailer which was added to enhance the fuel efficiency of a combined tractor/trailer combination. Many of the same principles that I’m already using such as side skirts and a trailer tail were added to promote fuel efficiency. What we are looking at here is an integrated truck, power-train and trailer.
I wanted to include the press release article from Freightliner as I didn’t want to miss anything about this amazing truck. It will be interesting to see how long it will be before many of these innovative technologies become main stream.
LOUISVILLE, Ky. – March 25, 2015 –Daimler Trucks North America’s (DTNA) SuperTruck program has achieved 115 percent freight efficiency improvement – surpassing the Department of Energy (DOE) program’s goal of 50 percent improvement and exhibiting the best results of all reporting OEMs. The SuperTruck was unveiled today at the 2015 Mid-America Trucking Show (MATS) in the Freightliner Trucks booth (#30125).
To validate the lofty targets set by the DOE, DTNA engineers conducted a series of tests. To measure freight efficiency, DTNA ran vehicle testing on highway routes in Oregon and Texas, one city route in Portland, Ore., and anti-idle testing in both a cold chamber and hot chamber. These tests resulted in a combined 115 percent freight efficiency improvement over a 2009 baseline truck.
Testing was also conducted at the DTNA Detroit engineering facility to demonstrate engine efficiency by achieving 50.2 percent engine brake thermal efficiency.
The final SuperTruck demonstrator ran a five-day, 312-mile round trip route on Texas Interstate 35 between San Antonio and Dallas, at a weight of 65,000 lbs GVWR at a speed of 65 mph, where it achieved an average result of 12.2 mpg.
“We are thrilled with the positive results, and are honored to have been part of the program,” said Derek Rotz, principal investigator for SuperTruck, Daimler Trucks North America. “It is our expectation that we will continue to review and refine what we’ve learned and achieved over the course of the SuperTruck initiative, and use that knowledge to bolster our leadership in fuel efficiency.”
Solutions of Tomorrow Today
Several commercially viable technologies developed in conjunction with the SuperTruck program have been introduced in DTNA production vehicles, including 6x2 optimization and the aerodynamic components found on the Freightliner Cascadia® Evolution and the integrated Detroit™ Powertrain.
Strategies such as downspeeding with a custom engine rating and using the predictive capabilities of Intelligent Powertrain Management (IPM) components such as pre-loaded 3D digital maps to control shifting and eCoast events also increased efficiency and economy.
“By incorporating a mix of available technologies with future innovations, we were able to use the SuperTruck program to take the first steps in seeing what may be technically possible and commercially viable,” said Rotz. “We still have a long road ahead to determine ultimately what will be successful and what will achieve the greatest efficiencies.”
One key initiative was exploring how the tractor and trailer should be designed and optimized as a single system, not separate units. DTNA engineers also examined the impact and opportunities for efficiency gains with tire partners.
Features such as energy-efficient, wide-based, low-rolling resistance single tires and highly engineered aerodynamic surfaces on the trailer also maximized efficiency.
“We took a clean-sheet approach and looked beyond just the vehicle and engine,” noted Rotz. “We examined and analyzed and tested every single angle on the truck and trailer in our quest to achieve the best results.”
Future Innovations
During the development of the SuperTruck, DTNA engineers investigated how high-risk, high-reward technologies used in other industries could be applied to Class 8 vehicles. Electrified auxiliaries, controlled power steering and air systems, active aerodynamics, a long-haul hybrid system, waste heat recovery and trailer solar panels were some of the items assessed.
“Part of our process included taking a deep dive into different systems to analyze not only what might be possible, but obstacles as well,” explained Rotz.
The SuperTruck team discovered that some of these components, due to regulatory or economic barriers, may not be commercially viable in the near future.
Added Diane Hames, general manager, marketing and strategy for Daimler Trucks North America: “The SuperTruck program is just one of many DTNA initiatives that underscore our deep commitment to developing and implementing best-in-class fuel efficiency and aerodynamic innovations that will benefit our customers and our industry for the long-term.”
About the SuperTruck Program
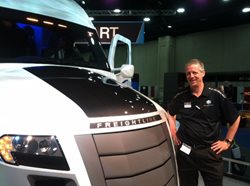 |
I would really like to see what kind of fuel mileage figures the Freightliner Super Truck and trailer could achieve on my regular route . |
Sponsored by the U.S. Department of Energy (DOE), the SuperTruck program was a five-year research and development initiative to improve freight efficiency by at least 50 percent, brake thermal efficiency by 50 percent, and reduce fuel consumption and greenhouse gas emissions of Class 8 trucks. DTNA and three other major truck OEMs were awarded multi-million dollar grants by the DOE and each matched the DOE funding dollar for dollar.
SuperTruck is supported by the U.S. DOE under the American Recovery and Reinvestment Act of 2009. DTNA began work on the SuperTruck program in 2010 together with Detroit and other partners, including national labs, universities and suppliers.